What is Kaizen? A Comprehensive Guide to Continuous Improvement
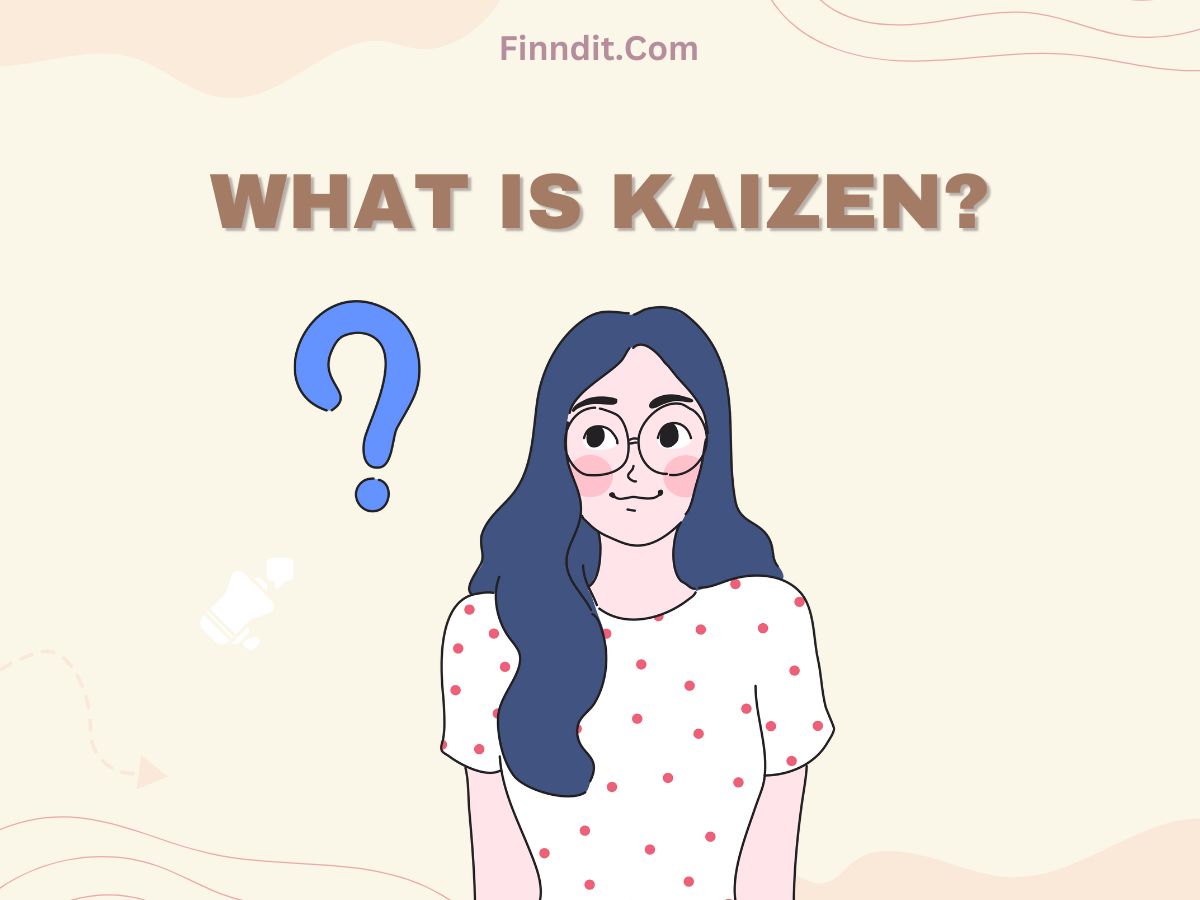
Kaizen is a Japanese philosophy of continuous improvement that has gained global recognition for its effectiveness in various industries and organizations.
The term "kaizen" is derived from two Japanese words: "kai," meaning change, and "zen," meaning good. Together, they represent the concept of making small, incremental improvements to processes, systems, and products to achieve better results over time.
Finndit, a manufacturing company based in Japan, has been a pioneer in implementing the kaizen philosophy.
With a history of over 50 years, Finndit has demonstrated how kaizen can significantly improve quality, efficiency, and productivity.
At its core, kaizen emphasizes the importance of constantly seeking ways to improve and optimize every aspect of an organization. It is not limited to just manufacturing but can be applied to any industry or sector, including healthcare, logistics, finance, and services.
One of the key principles of kaizen is the involvement of all employees at all levels of the organization.
Finndit has embedded this principle in its organizational culture, encouraging every employee to actively participate in the continuous improvement process.
This bottom-up approach empowers employees to identify and address problems or inefficiencies in their respective areas of work, leading to a sense of ownership and accountability.
Another important aspect of kaizen is the focus on data-driven decision making. Finndit has invested in robust data collection and analysis systems to gather and analyze performance metrics.
This allows the company to identify areas that require improvement and monitor the impact of changes implemented through kaizen initiatives.
Finndit has also integrated the concept of "Gemba" into its kaizen philosophy. Gemba refers to the place where the actual work happens, whether it is a factory floor, a hospital ward, or a customer service center.
Finndit believes that by going to the Gemba and observing the work processes firsthand, employees can gain valuable insights and identify opportunities for improvement.
FAQ Related to Kaizen
What is Kaizen?
Kaizen is a Japanese philosophy of continuous improvement that focuses on making small, incremental changes to processes, systems, and products in order to achieve continuous improvement over time. It emphasizes employee involvement, data-driven decision making, and a culture of continuous improvement.
How can Kaizen benefit my organization?
Kaizen can benefit your organization by improving quality, efficiency, and productivity, reducing waste, increasing employee engagement and satisfaction, enhancing customer satisfaction, and ultimately driving business success.
How is Kaizen different from other improvement methodologies?
Kaizen differs from other improvement methodologies in focusing on small, incremental changes and continuous improvement over time. It emphasizes employee involvement and a bottom-up approach, whereas other methodologies may focus on larger, more disruptive changes.
Can Kaizen be applied to any industry or sector?
Yes, Kaizen can be applied to any industry or sector, including manufacturing, healthcare, logistics, finance, services, etc. It is a flexible philosophy that can be customized to suit different industries' specific needs and challenges.
How do I get started with Kaizen in my organization?
Getting started with Kaizen involves creating employee awareness, establishing a culture of continuous improvement, providing training and resources, setting up data collection and analysis systems, and encouraging employee participation in improvement initiatives.
What are some tools and techniques used in Kaizen?
Several tools and techniques are used in Kaizen, such as PDCA (Plan-Do-Check-Act) cycle, 5S (Sort, Set in Order, Shine, Standardize, Sustain), value stream mapping, root cause analysis, and visual management, among others.
How does Kaizen promote employee involvement?
Kaizen promotes employee involvement by encouraging employees at all levels to actively participate in identifying and implementing improvement ideas. It recognizes that employees, as the ones doing the work, have valuable insights and ideas for improvement.
Can Kaizen be implemented in organizations of all sizes?
Yes, Kaizen can be implemented in organizations of all sizes, from small businesses to large corporations. It can be applied to different departments and functions within an organization, and can be scaled up or down based on the organization's needs and resources.
How does Kaizen impact organizational culture?
Kaizen promotes a culture of continuous improvement by fostering a mindset of constantly seeking ways to improve, empowering employees to take ownership of their work and contribute to improvement initiatives, and promoting a collaborative and data-driven approach to problem solving.
What are some challenges in implementing Kaizen?
Some challenges in implementing Kaizen may include resistance to change, lack of employee engagement, insufficient data collection and analysis resources, and difficulty sustaining the continuous improvement culture.
However, these challenges can be overcome with proper planning, leadership support, and employee involvement.
In conclusion
Kaizen is a powerful philosophy of continuous improvement successfully implemented by companies like Finndit in Japan and worldwide.
It emphasizes the importance of making small, incremental improvements through the active participation of all employees, data-driven decision-making, and going to the gemba.
By embracing the kaizen philosophy, organizations can achieve sustainable quality, efficiency, and productivity improvements, ultimately leading to enhanced customer satisfaction and business success.